Wenn in der Nachbarschaft mal wieder in Kind laut rumpelnd die Straße entlang rollt, dann sollten sich genervte Ohrenzeugen über eines im Klaren sein: Hinter dem Geräusch verbirgt sich etwas Kleines, was vor 50 Jahren groß geworden ist - das Bobbycar. Das rollende Spielzeug, das hierzulande Generationen geprägt hat. Wie es gebaut wird, ist im mittelfränkischen Burghaslach zu erleben.
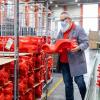
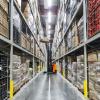
Pro Jahr 4000 Tonnen Plastik und ein Stromverbrauch wie ein ganzes Dorf - Fakten rund ums Bobbycar bündeln sich am Rand der beschaulichen Steigerwaldgemeinde in bis zu 40 Meter hohen Hallen, die von der nur wenige hundert Meter entfernten Autobahn Würzburg-Nürnberg (A3) gut zu sehen sind.
Es ist die BIG-Spielwarenfabrik, vor der ein überdimensionales, knallrotes Bobbycar steht und von der aus das Plastik-Rutschauto mit seiner Quietsche-Hupe und dem rumpelnden Fahrgeräusch in die ganze Welt gebracht wird. 2000 Stück verlassen pro Tag das Werk. Sie fahren hinaus in eine Welt, in der es mittlerweile Fanclubs mit erwachsenen Kindern gibt, die Bobbycars aufmotzen und damit sogar bei Weltmeisterschaften um die Wette rollen.
Am 5. Februar 1972 stand das Bobbycar auf der Nürnberger Spielwarenmesse zum ersten Mal im Scheinwerferlicht. Diese 50 Jahre feiern die Fürther Firmengruppe Simba-Dickie und das Tochterunternehmen BIG heuer unter anderem mit einer Bobbycar-Sonderausgabe: Es ist ein besonders schnittiges Exemplar geworden mit modernem Design. Doch die Grundelemente des Miniautos sind in all der Zeit unverändert geblieben.
190 Menschen arbeiten von montags bis freitags in je drei Schichten in der Bobbycar-Fabrik, manchmal sind auch samstags die Maschinen an. Auch andere Plastikspielzeuge entstehen hier, doch das Rutschauto dominiert eindeutig.
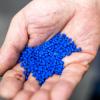
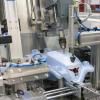
20 Millionen Stück sind laut BIG in den vergangenen 50 Jahren hergestellt worden. Würde man sie in einer Reihe aufstellen, dann reichte der Stau von Burghaslach bis an die Nordküste von Australien. Was das Unternehmen da ausgerechnet hat, wird in der Burghaslacher Fabrik nachvollziehbar: Im Minutentakt holen Roboter-Greifarme die Bobbycar-Rohformen aus zehn Spezialmaschinen.
Was das Bobbycar mit einem Thermomix-Gerät zu tun hat
Diese Maschinen haben oben einen Aufsatz, der einem Küchengerät à la Thermomix ähnelt. Dort hinein wird aus zehn großen Silos und durch 200 Meter lange Rohre Plastikgranulat geblasen, das wie bunter Hirsebrei aussieht.
Eine Art Mini-Backofen in dem Aufsatz lässt das Granulat bei 200 Grad Celsius zu einer weichen Kunststoffwurst schmelzen, die kurz darauf nach unten in eine Form rutscht. Diese Form hat die Konturen des Bobbycars.
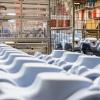
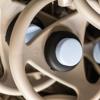
Was das Besondere am Bobbycar-Lenkrad ist
Mit einem Luftdruck von 7 bar - ein herkömmlicher Autoreifen hat 2,5 - wird die weiche, warme Plastikwurst in der geschlossenen Form aufgeblasen, so dass sich die Kunststoffschicht gegen Innenseiten presst. Nach einer kurzen Abkühlung gibt die Form das Kunststoffgebilde für die Roboter-Greifarme frei: Ein neues Bobbycar ist fertig, zumindest grob.
Was folgt, sind weitgehend automatisierte Schritte: Förderbänder und Greifarme bringen die Rohformen dorthin, wo die Achsen und Plastikräder montiert werden. Später schieben BIG-Beschäftigte das fertige Spielzeug in Kartons und legen das Lenkrad dazu.
Weil es für die Verpackung hinderlich ist, muss es später vom Käufer selbst auf die Lenkachse gesteckt werden. Ein Handgriff, den Scharen von Eltern mit Sicherheit kennen.
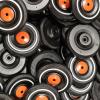
Porsche, Daimler oder Quad: Hauptsache Bobbycar
Sechs Grundtypen des Bobbycars in insgesamt 22 Varianten gibt es mittlerweile. Vom Porsche- oder Daimler-Imitat über ein Quad bis hin eben zum knallroten Klassiker haben alle Rutschauto eines gemeinsam: Sie wiegen 1,5 Kilo, sind hohl und aus Polyethylen, dem in unserem Alltag gängigsten Kunststoff.
Er wird von Lieferanten aus ganz Europa nach Burghaslach gebracht. 4000 Tonnen Granulat pro Jahr. Das ist das Gewicht von etwas mehr als 600 ausgewachsenen Elefanten. Alternativen zum herkömmlichen Plastik sieht BIG nicht. 2017 habe das Werk in Burghaslach versucht, Recycling-Kunststoff einzusetzen, erklärt Produktionsmanager Andreas Blank. Wegen der komplexen Anforderungen an das Material beim Einsatz für das Bobbycar habe sich dieses Material aber nicht bewährt.

Burghaslacher Werk: Blockheizkraftwerk und ein gewisser Umweltgedanke
Um trotzdem dem Umweltgedanken Rechnung zu tragen, hat das Werk auf der Wiese nahe der A3 ein eigenes Blockheizkraftwerk, das laut Blank die Hälfte des immensen Strombedarfs abdeckt. Zudem, sagt der Produktionsmanager, werde sämtlicher Plastikabfall rund um die Bobbycar-Herstellung sowie Ausschussware geschreddert und der Produktion zugeführt.
320 000 Quadratmeter Fläche hat das Werksgelände, das ist die Größe von 45 Fußballfeldern. Vieles davon sei noch frei, betont Blank. Eine Vergrößerung des Werks also durchaus machbar. Ein Indiz dafür, dass das Bobbycar seine Erfolgsfahrt wohl noch eine ganze Weile fortsetzt.
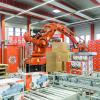
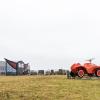