Die Bosch Rexroth AG ist einer der größten Arbeitgeber Mainfrankens. Ihre Gießerei in Lohr ist ihr Herzstück. Seltene Blicke in Hallen, die was von Hölle haben.
So muss es in der Hölle sein: gleißende Glut in großen Pötten, Funkenflug und vom Ruß geschwärzte Hallen. Es riecht nach rauchigem Metall.
Gut 400 Menschen in Lohr sehen das ganz anders: Für sie sind die Hallen ihr Arbeitsplatz. Mehr noch: Die Gießerei von Bosch Rexroth ist Wiege und Herzstück dieses Industrieunternehmens, das mit 7300 Beschäftigten an vier mainfränkischen Standorten einer der größten Arbeitgeber in der Region ist.
Wer die Helden sind in der Gießerei von Bosch Rexroth
Die eigentlichen Helden der Gießerei sind Männer wie Toby Pitzky. Er sitzt in einem mit Digitaltechnik vollgepackten Fahrzeug, das einem wuchtigen Gabelstapler ähnelt. Auf mehreren Displays sieht er alle wichtigen Infos für seinen Job.
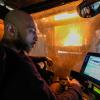
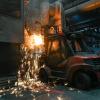
Durch die matten Scheiben des Staplers hat Pitzky in den dunklen Hallen nicht die beste Sicht. Die bräuchte er vielleicht, um mit seinem Fahrzeug tonnenschwere Behälter zentimetergenau unter jene Öffnung zu platzieren, aus der der Hochofen kurz darauf das 1500 Grad heiße Gusseisen fließen lässt.
Wenn Pitzky mit dem vollen Behälter dann einige Meter weiter an der nächsten Station hält, wird gute Sicht noch wichtiger. Denn dann muss der Fahrer den wuchtigen Pott so kippen, dass das Metall in eine nur 50 Zentimeter große Öffnung fließt.
Wenn Pitzky da nicht genau arbeitet, "kann es rundherum eine ziemliche Sauerei geben", schmunzelt Fertigungsleiter Wörner. Er kann sich das Schmunzeln leisten, denn es passiere selten, dass was daneben geht. Pitzky beherrsche seinen Job genauso wie die anderen Fahrer – matte Scheiben am Gabelstapler hin oder her.
Lohrer Gießerei: Wie einst im Ruhrgebiet
Die Gießerei mitten in der Lohrer Innenstadt hat jene archaische Aura der Hochöfen einst im Ruhrgebiet. Dass Metall in großem Stil gegossen wird, gibt es im ansonsten nicht von Schwerindustrie geprägten Mainfranken etwa bei Frankenguss in Kitzingen, bei Düker in Karlstadt, bei Koenig & Bauer in Würzburg, bei Coatinc im benachbarten Rottendorf oder bei Schaeffler in Schweinfurt.
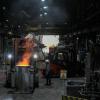
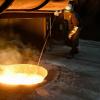
In dieser Reihe hebt sich die Lohrer Gießerei durch ihre Geschichte hervor. Der Eisenguss der Familie Rexroth ist im Spessart schon seit Ende des 18. Jahrhunderts bekannt.
Stellenwert und Wertschätzung hat er bis heute: Die international aufgestellte Bosch Rexroth AG steckt seit Monaten mehrere Millionen Euro in diese Fertigung, um sie zu sanieren und voranzubringen.
Freilich hat die Gießerei vor wenigen Tagen für andere Schlagzeilen gesorgt, weil dort ab Juni wegen eines Auftragsrückgangs für sechs Monate Kurzarbeit gilt. Die Delle sei aber vorübergehend, sagte ein Sprecher.
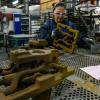
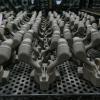
Neues Kühlhaus in der Gießerei lässt Bosch Rexroth CO2 vermeiden
Abgesehen davon ist der hohe Stellenwert der Gießerei seit Mitte März zum Beispiel am neuen Kühlhaus der Gießerei zu erkennen. Es ist eine Art Hochregallager für jene Metallteile, die frisch aus dem Hochofen kommen.
Bislang sei der Abkühlvorgang an ein externes Unternehmen vergeben worden, erklärt Gießerei-Leiter Totnan Bald. Aus technischen Gründen habe dafür das Metall aber kurzzeitig wieder auf 900 Grad hochgeheizt werden müssen.
Dieser Extra-Aufwand falle nun weg, der Abkühlprozess in dem neuen Gebäude sei zudem schneller, so Bald. Einen Ökö-Nebeneffekt gibt es zudem: Nach Firmenangaben verringert das Kühlhaus den CO2-Ausstoß der Lohrer Gießerei um 2000 Tonnen pro Jahr.
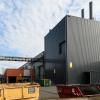
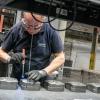
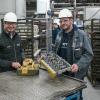
Hochöfen der Gießerei laufen rund um die Uhr
Was in den drei Hochöfen an fünf Tagen pro Woche rund um die Uhr geschmolzen und später in Formen gegossen wird, hat für Bosch Rexroth zentrale Bedeutung: Die für Hydraulikapparate zum Beispiel in Baggern oder Schleusentoren gedachten Metallteile gehen in alle deutschen Werke des Unternehmens - und zum Teil in alle Welt.
Die Dimensionen sind enorm: 30.000 Tonnen Metall werden pro Jahr in Lohr geschmolzen. So viel wiegen 30.000 Kleinwagen à la Opel Corsa. An jedem Arbeitstag verlassen 312 Tonnen Flüssigmetall die mit Strom betriebenen Öfen.
Es sei grüner Strom, betonen Gießerei-Leiter Bald und Fertigungsleiter Markus Wörner. Wie viel Strom das Werk pro Jahr benötigt, verrät Bosch Rexroth im Detail nicht. Nur so viel: Der Verbrauch sei "in etwa so hoch wie der einer kleinen Stadt".
Was genau geschmolzen wird, ist geheim
Betriebsgeheimnis ist auch die Metall-Mixtur in den Hochöfen. Das sei wie ein Küchenrezept zu verstehen, sagt Totnan Bald. Die Zutaten lagern in einer riesigen Nebenhalle der Gießerei: Metallschrott verschiedener Art, bis zu 90 Prozent Recyclingware, zum Teil Ausschussware des eigenen Werks.
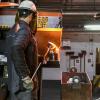
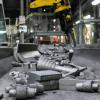
Damit das Rezept stets stimmt, werden regelmäßig Proben gezogen. Ein Apparat misst zum Beispiel, wie viel Kohle, Silizium oder Mangan in der Metallmixtur ist. Diese Daten seien "ganz wesentlich" für die Qualität der zu gießenden Teile, erklärt Bald.
Was es bei Bosch Rexroth mit Modellbauern und Kernen auf sich hat
Eine Dreiviertelstunde dauert es, bis ein Ofen seine 13-Tonnen-Ladung Metallschrott flüssig gemacht hat. Eine Station weiter fließt das Gusseisen in mit Spezialsand gefüllte Behälter. Darin befinden sich von Modellbauern hergestellte Kerne, wie die Rexröther sagen.
Diese Skulpturen sind das Negativ jenes Gegenstandes, um den es letztendlich geht: Wo kein Gusseisen hinfließen kann, sind gewollte, röhrenartige Hohlräume. Durch sie soll später zum Beispiel in Baggermotoren oder Schleusentoren Hydrauliköl fließen.